
Share this story
Success in the changing landscape of the construction industry hinges on careful management of our supply chain. Lessons learnt from our Morris Moor and Scape projects highlight the importance of conducting factory visits and inspections during a build. Our lessons from our factory visits are shared companywide to ensure we all learn from them, and in sharing our insights externally, we hope you will too!
Gaining invaluable insights into the manufacturing process
During our Morris Moor project, we conducted regular factory visits including to our steel production supplier, and precast manufacturers. These visits have allowed us to gain a better understanding of the manufacturing process, providing insights into lead times, production capacity, and assembly complexity. By physically witnessing the manufacturing process, we have developed a deeper appreciation for the intricacies involved, which helps in making informed decisions back on site.
Building strong rapport with suppliers and subcontractors
Another critical aspect of conducting factory visits is the opportunity to build better relationships with subcontractors and suppliers. By being physically present in the factory, project managers and stakeholders establish rapport and foster open communication channels. This relationship can be an asset when issues arise, as it encourages greater transparency and collaboration.
Ensuring accountability
One of the most significant benefits of factory visits is ensuring accountability. The case of Scape perfectly illustrates this. When we discovered that our pre-caster was struggling to meet production demands we had outsourced to another manufacture. The site team insisted on visiting the factory personally to ensure the process was on track. Upon inspection, we found that panels were missing, which could have potentially led to costly delays. Our insistence on visiting the factory and conducting stock-checks uncovered the issue, preventing a significant setback.
Cost savings and time efficiency
The story from Scape highlights how a single factory visit saved us from potential losses of up to $100,000 in delay costs. This cost-saving is not just about the financial aspect; it's also about the invaluable time that might otherwise be consumed in addressing an issue that should have been prevented. Our Morris Moor project team were able to identify potential issues with materials prior to them being sent to site, saving time for the project. Through our on-site factory visits, our team effectively sidestepped potential disruptions to our project timeline, allowing us to stay on track.
Trust but verify
The Morris Moor team were provided the opportunities through conducting site visits where they could see and verify the status of manufacture. Multiple experiences have been shared where a factory is expected to have products nearing completion and ready to be delivered to site, only for the factory visit to discover that the manufacturer is behind schedule. The key lesson learnt from these experiences is the saying, "trust but verify." Regardless of the promises made by subcontractors and suppliers, a physical visit to the factory is essential to confirm the progress and quality of the work. This principle applies to all suppliers and materials being procured or manufactured off-site. It's a vital part of risk management in the construction industry.
Gaining invaluable insights into the manufacturing process
During our Morris Moor project, we conducted regular factory visits including to our steel production supplier, and precast manufacturers. These visits have allowed us to gain a better understanding of the manufacturing process, providing insights into lead times, production capacity, and assembly complexity. By physically witnessing the manufacturing process, we have developed a deeper appreciation for the intricacies involved, which helps in making informed decisions back on site.
Building strong rapport with suppliers and subcontractors
Another critical aspect of conducting factory visits is the opportunity to build better relationships with subcontractors and suppliers. By being physically present in the factory, project managers and stakeholders establish rapport and foster open communication channels. This relationship can be an asset when issues arise, as it encourages greater transparency and collaboration.
Ensuring accountability
One of the most significant benefits of factory visits is ensuring accountability. The case of Scape perfectly illustrates this. When we discovered that our pre-caster was struggling to meet production demands we had outsourced to another manufacture. The site team insisted on visiting the factory personally to ensure the process was on track. Upon inspection, we found that panels were missing, which could have potentially led to costly delays. Our insistence on visiting the factory and conducting stock-checks uncovered the issue, preventing a significant setback.
Cost savings and time efficiency
The story from Scape highlights how a single factory visit saved us from potential losses of up to $100,000 in delay costs. This cost-saving is not just about the financial aspect; it's also about the invaluable time that might otherwise be consumed in addressing an issue that should have been prevented. Our Morris Moor project team were able to identify potential issues with materials prior to them being sent to site, saving time for the project. Through our on-site factory visits, our team effectively sidestepped potential disruptions to our project timeline, allowing us to stay on track.
Trust but verify
The Morris Moor team were provided the opportunities through conducting site visits where they could see and verify the status of manufacture. Multiple experiences have been shared where a factory is expected to have products nearing completion and ready to be delivered to site, only for the factory visit to discover that the manufacturer is behind schedule. The key lesson learnt from these experiences is the saying, "trust but verify." Regardless of the promises made by subcontractors and suppliers, a physical visit to the factory is essential to confirm the progress and quality of the work. This principle applies to all suppliers and materials being procured or manufactured off-site. It's a vital part of risk management in the construction industry.
Latest News
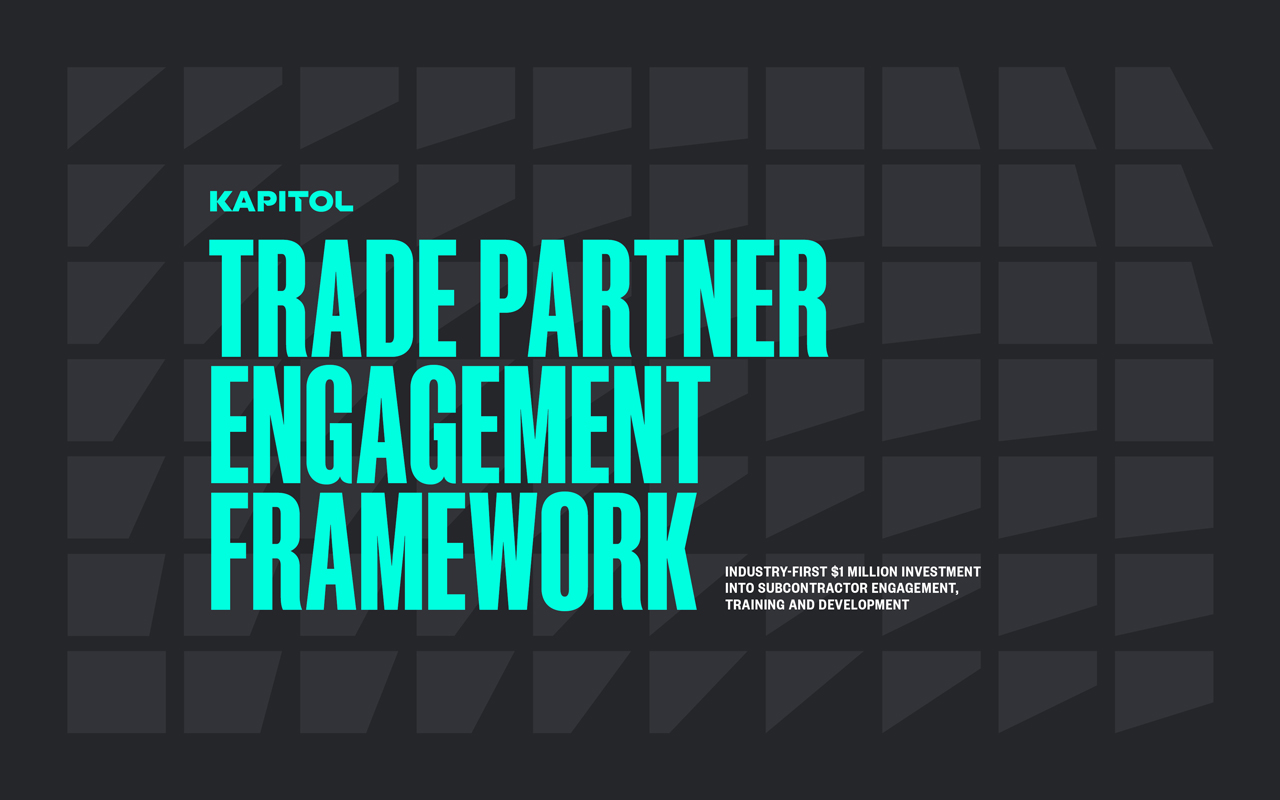
Kapitol's New Construction Trade Partner Framework
As one of Australia's fastest-growing construction firms, Kapitol is excited to announce the launch of its new Trade Partner Engagement Framework.

Kapitol Becomes Platinum Partner of the Western Bulldogs
Strength, teamwork, and ambition — Kapitol joins the Western Bulldogs as a Platinum Partner, with branding on the AFL team’s guernseys from 2025.
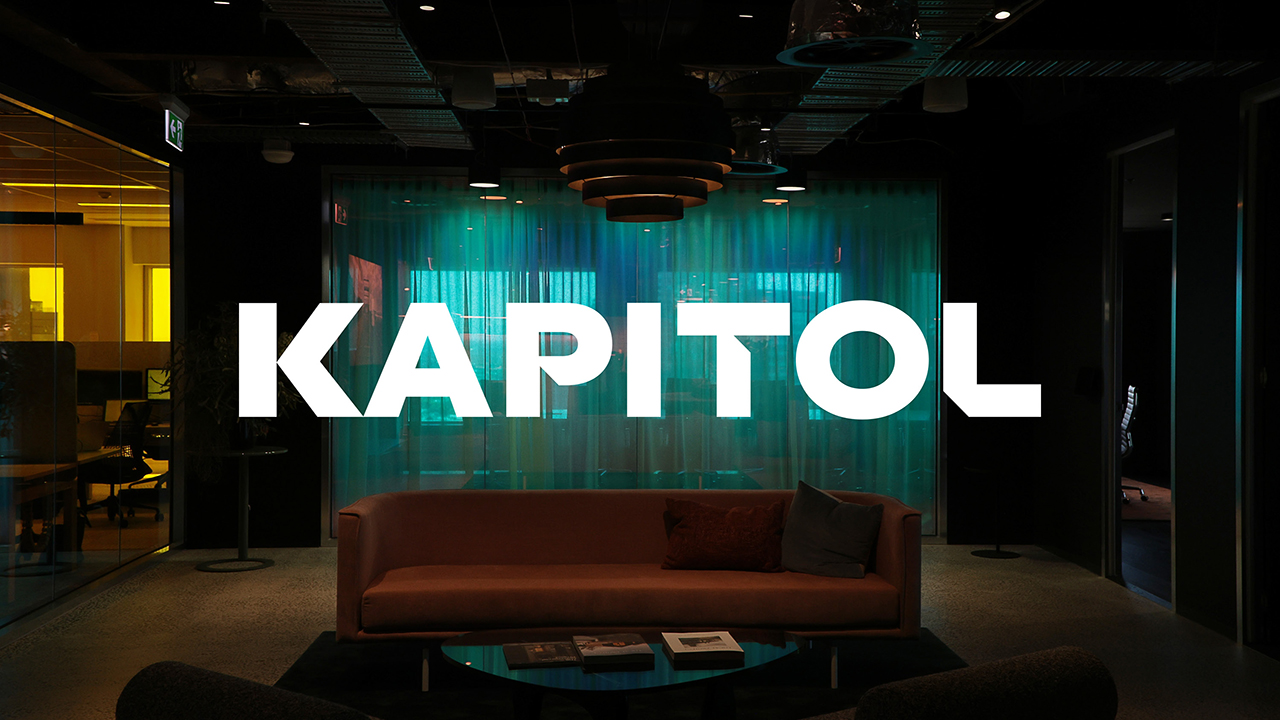.jpg?lang=en-US&ext=.jpg)
Kapitol’s New Era: Bold Rebrand and Vision
Kapitol’s bold rebrand reflects our rapid growth, innovation, and commitment to delivering exceptional construction outcomes.