Construction’s Digital
Technology Experts
At Kapitol Group, our dedicated in-house team of design managers, digital engineers, and architects is pioneering digital innovations in the construction industry.
Driven by a passion for advancement and a commitment to efficiency, we are committed to leading digital innovations in the construction industry, delivering substantial benefits to all our clients and stakeholders, including those in the ASX-listed data centre technology sector.
Our Digital Engineering team are an integral part of the construction workflow and consists of three specific sub-teams that each bring their own unique skillsets. These teams collaborate seamlessly to integrate innovative solutions throughout every step of the project phase to ensure we deliver quality projects in an efficient manor, that are beyond our clients’ expectations. Read more below about what each of our team's do.
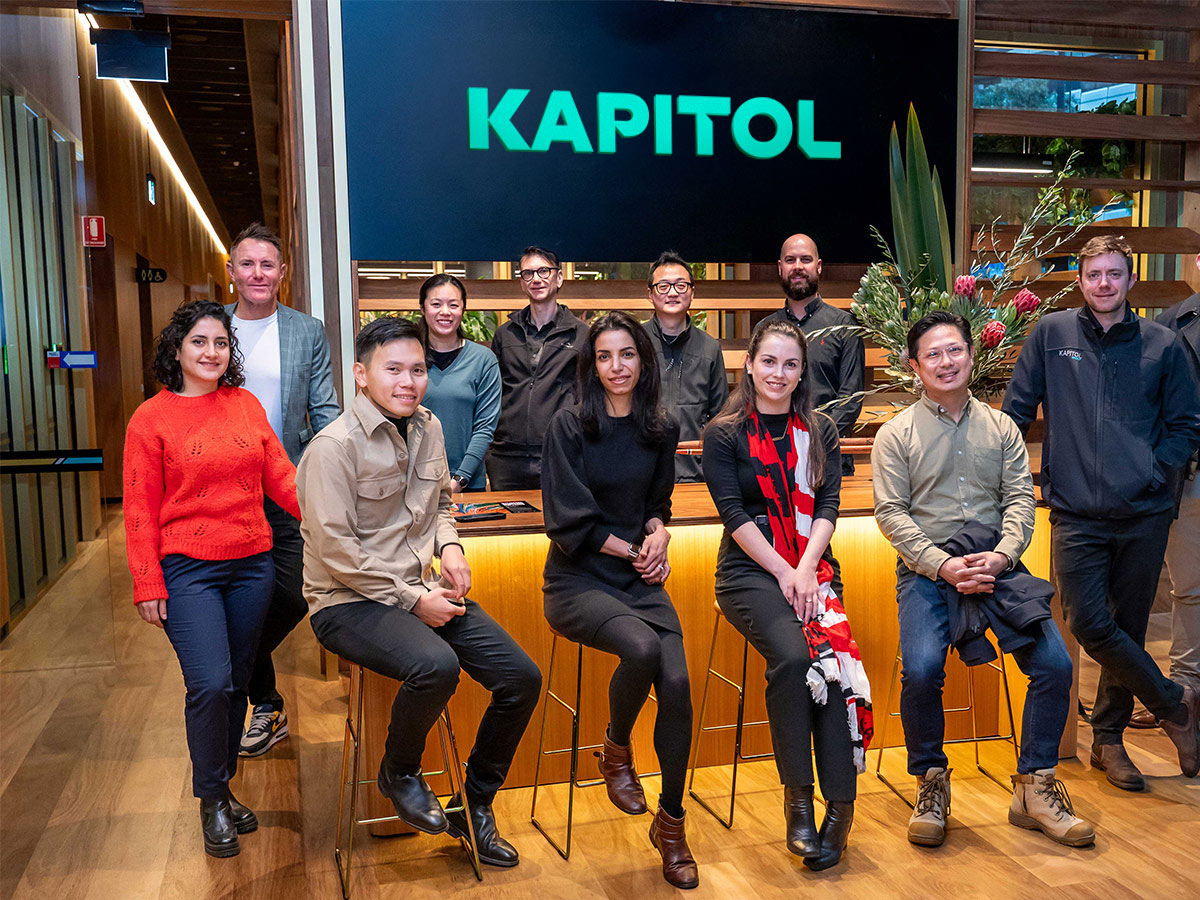
Virtual Design & Construction Team
The Virtual Design & Construction (VDC) team’s responsibilities include the integration of Building Information Modelling (BIM), which leverages state-of-the-art digital tools and methodologies to enhance project coordination and ensure buildings are clash free in the virtual world, prior to being built on-site.
Digital Technology Automation Team
The Digital Technology Automation (DTA) team is dedicated to developing and maintaining a suite of bespoke digital tools to enhance productivity across all phases of construction projects. This includes PowerBI dashboards, material construction trackers, design & coordination trackers, and other bespoke applications, to enhance productivity.
Their work is pivotal in providing real-time insights and analytics, which enable efficient resource management, timely decision-making, and enhanced coordination among project teams.
Architectural Team
The Architectural team oversee all aspects of the 2D architectural drawings and specifications, which form the backbone of the construction documentation process. The architectural team plays a critical role in preventing costly errors and delays, thus safeguarding the project's integrity, and ensuring a seamless transition from design to execution.
Building better, faster, safer: the digital advantage
The benefits are resounding. Click on each section to learn more about how our industry-leading, in-house digital engineering capabilities enhances our construction projects.
Kapitol Group has committed to the implementation of Building Information Modelling (BIM) across all projects, regardless of project size or complexity. This proactive digitisation in design and construction anticipates and resolves potential issues, such as clash detections, before they impact the site.
By utilising Point Cloud Scan technology, Kapitol accurately captures and verifies existing site conditions, ensuring that design documentation is perfectly aligned with the physical site. This accuracy is crucial for streamlining procurement and the preparation of shop drawings for items requiring long lead times. Additionally, this technology is instrumental in validating as-built models, validating that all 3D models precisely represent the elements installed on-site. This process provides clients with a reliable digital twin model, offering a comprehensive digital representation of the physical space.
Mobile technology is pivotal in transforming our construction sites into highly efficient, connected environments. We equip our project teams with advanced mobile applications and devices that ensure immediate access to crucial project documentation, deliver real-time updates, and enable thorough on-site inspections. This technology facilitates seamless and constant communication among all project participants, which supports faster decision-making and superior project management, driving productivity and ensuring project success.
In parallel, our use of Building Information Modelling (BIM) technology includes advanced 3D clash detection across all design disciplines. By identifying discrepancies and areas requiring coordination early in the design process and throughout the trade’s engagement period, we prevent conflicts before construction begins. This method significantly reduces the risk of costly and time-consuming modifications during critical project phases. The integration of clash detection tools into our BIM processes ensures that potential issues are resolved promptly, streamlining project execution, and ensuring a smoother construction phase with fewer interruptions.
These revisions aim to articulate the specific processes and benefits of both 2D design documentation review and 3D BIM clash detection more distinctly, underlining their integral roles in improving project delivery and reducing risks.
Our adoption of 4D sequencing elevates project management by visualising and optimising project timelines, effectively identifying potential conflicts, and enhancing coordination across teams. The integration of high-risk activities modelling and sequencing animations into our project workflow allows us to proactively manage risks. This strategic approach not only improves safety measures but also minimises the likelihood of project delays. By foreseeing and addressing challenges before they materialise, we ensure smoother and safer project execution.
We employ a suite of digital platforms that help to facilitate and enhance our project delivery. Our customised, integrated dashboards provide live reporting and complete transparency on key project deliverables, fostering a collaborative working environment and optimising overall project health.
Our team leverages advanced analytics to meticulously analyse large volumes of construction data. By deploying sophisticated data processing techniques, we extract valuable insights that enable predictive analytics, enhance outcome forecasting, and facilitate robust risk identification. This strategic application of analytics is pivotal in optimising construction processes, significantly boosting project efficiency, and effectively mitigating potential risks. As a result, our approach not only streamlines project workflows but also substantially improves performance and reliability across all our construction initiatives.
We rigorously review all architectural and engineering documentation to ensure they accurately reflect the project's requirements and are free from any errors or ambiguities. This diligent verification process helps prevent misunderstandings and the subsequent cascade of change orders, thus minimising RFI processing and associated costs. Our proactive review strategy not only expedites approvals but also enhances project workflow efficiency, ensuring that construction can proceed without preventable delays.
Throughout the design and construction phases, our advanced digital modelling process employs LiDAR scanning to accurately capture and validate 3D models against as-built conditions. This approach not only ensures the accuracy of the models but also provides an LOD500 digital twin—an exact digital representation of the as-built conditions. This high level of detail is increasingly demanded by asset owners for its definitive accuracy in As-Built documentation. Such comprehensive digital twin models are invaluable for facilities management, enabling clients to efficiently plan, manage, and maintain their assets.
At Kapitol Group, we enhance our quality control and record management processes through the integration of OpenspaceAI. This innovative technology synchronises our project models with on-site walkthrough cameras, improving how we monitor and manage construction quality. By aligning real-world conditions with our detailed designs, OpenspaceAI enables us to quickly identify and address any design discrepancies. This alignment not only ensures adherence to design specifications but also significantly improves the accuracy and efficiency of our projects.
How we’re using 3D modelling
For Prefabrication and Modular Construction
Modular BIM Model
Kapitol Group utilises digital technologies such as BIM 3D modelling to enhance our off-site prefabrication and modular construction processes. This strategic use of technology ensures high precision throughout the design, manufacturing, and assembly stages. By improving these key phases, we significantly boost operational efficiency and project control while reducing waste. The result is a streamlined construction process that not only meets but exceeds industry standards for quality and sustainability.
For Improving Construction Safety
Temporary Safety Structure BIM Model
Our digital engineering team uses the latest digital applications to manage models across all aspects of our projects. This approach is specifically focused on improving safety measures during construction. By applying detailed modelling to high-risk activities, clearance zones, and safety equipment design, we proactively address potential safety issues. This method ensures that every phase of construction is planned with the highest attention to safety, reducing risks and safeguarding all site personnel.
By establishing a robust BIM environment throughout the design and construction phases, we believe Kapitol Group is well placed to manage integration of digital technologies at every step of the project lifecycle.
Meet our Digital Engineering Team
Watch Digital Engineering in Action!
See how Kapitol Group's Digital Engineering Team use a variety of technology on our construction projects to improve efficiency and quality and safety outcomes, from 4D sequencing to using BIM to model temporary rails.