The power of collaboration
Kapitol Group’s expertise in Early Contractor Involvement (ECI) is a testament to the power of client collaboration for the successful delivery of construction projects. ECI projects account for more than 50% of our workbook which spans across industrial, residential, commercial, education, infrastructure, and health sectors.
During ECI engagement, we take the client on a journey with us. We first seek to understand key success criteria for the project and then work collaboratively to identify efficiencies in design, as well as advising on buildability and logistics, to reduce program and cost whilst maintaining design intent and ensuring safe and quality outcomes.
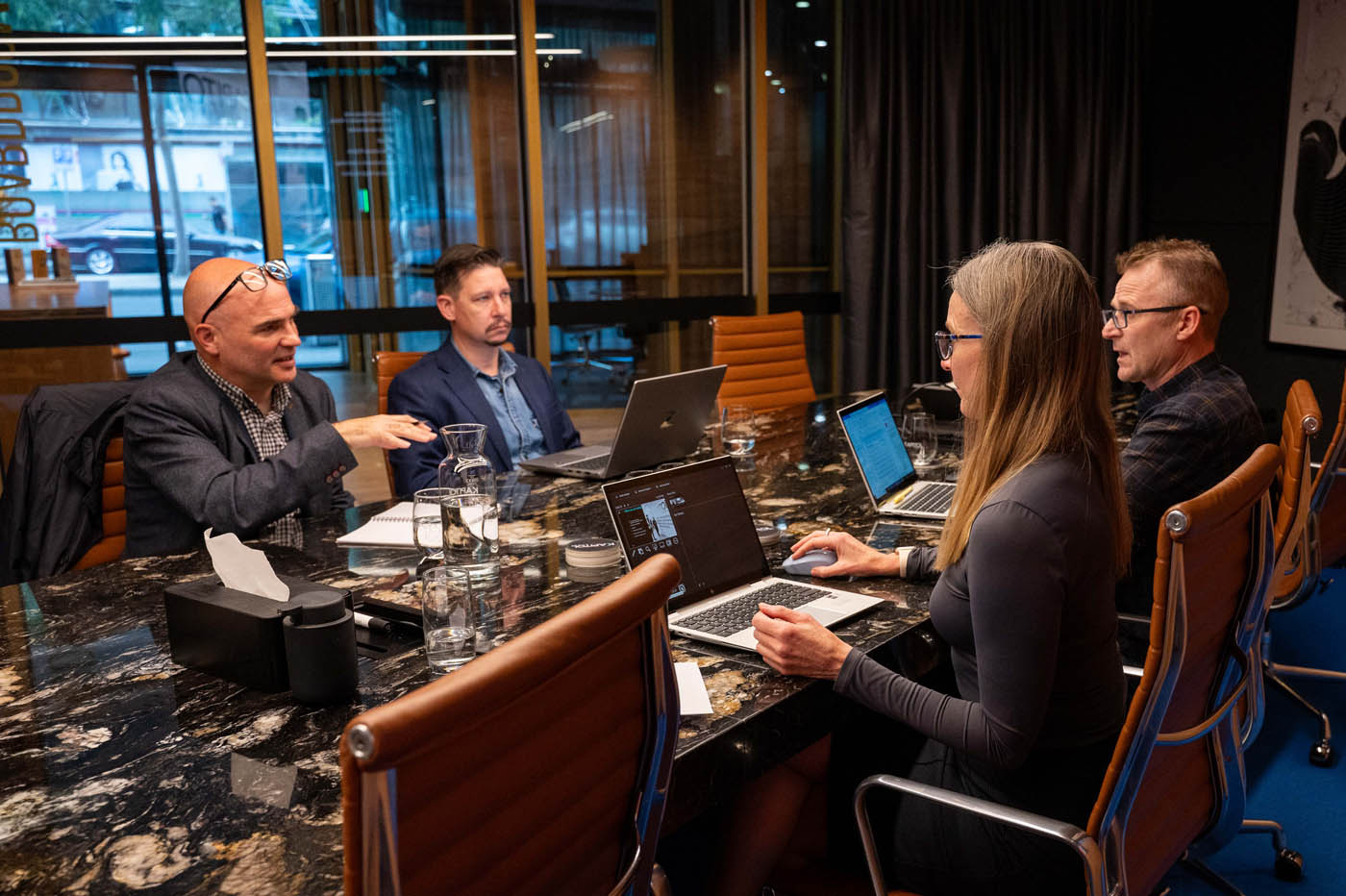
“Kapitol approaches ECI differently to most. From the outset, we adopt an open-book method of negotiation providing full transparency into our costing process with the aim of achieving the ultimate commercial, safety, quality outcomes for our clients. As part of this process, we engage trades and never leave anything to chance. This is why our ECI approach is favoured by our top ASX listed clients.”
Andrew Deveson, Director, Kapitol Group
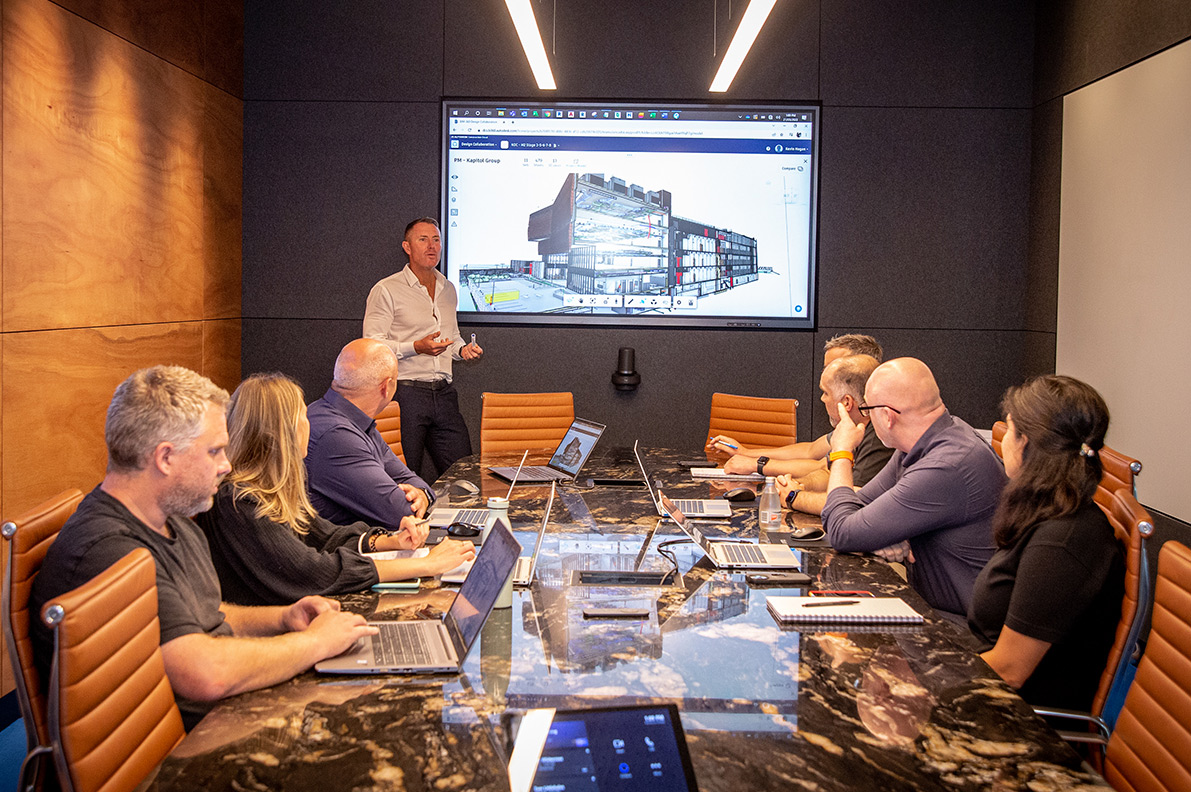
Kapitol's ECI team
Kapitol Group’s ECI team draws expertise from various parts of the organisation:
Project Managers - work with planners, estimators, design managers, SMEs, Digital Engineers, and advisors to ensure the best outcome for the ECI,
Planners - find efficiencies in programming and logistics,
Estimators - work with trades to ensure we provide realistic costs,
Construction Advisors - advise on construction sequencing and logistics,
Design Managers - review materiality and overarching design to efficiencies and ensure compliance requirements are met,
Digital Engineers - review available 3D models to identify and resolve clashes between architecturals (spatials), structure and services
SME’s including Façade, Structure, Fire and Services Experts review documentation to identify any risks,
Quantity Surveyors - ensure measures are accurate and work with Estimating on accurate cost planning
Our inhouse team doesn’t work in a silo to develop “best guess” results. Instead, we work collaboratively with trade partners, QS’s, PMs, and design consultants during the ECI process to develop efficient designs in line with our clients’ goals.
Getting the contractor involved early and leveraging their expertise may help identify and resolve buildability issues before they become costly, and could open the door for value engineering, better risk allocation, design optimisation and overall better 'bang for buck'. The ECI approach might take longer at the very front end of the project, but it could also compress the overall duration due to fewer pre-contract clarifications, less rework, and more opportunities to overlap some activities.
Nicole Trumbull, National Director, WT (Australia)
The benefits of ECI
For clients | For consultant teams | For builders |
De-risk feasibility | Ongoing builder and trade insight | De-risk D&C |
Minimise cost | Design peer review | Validate budget |
Maximise Net Lettable Area (NLA) | Support from PM & QS | Improve buildability |
Improve programme | Iterative design development | Improve programme |
Reduce price volatility | Improve consultant outputs | Improve trade understanding and relationships |
Reduce risk overall | Early efficiencies and averted issues |
Hear about our ECI journey with HDR Architects
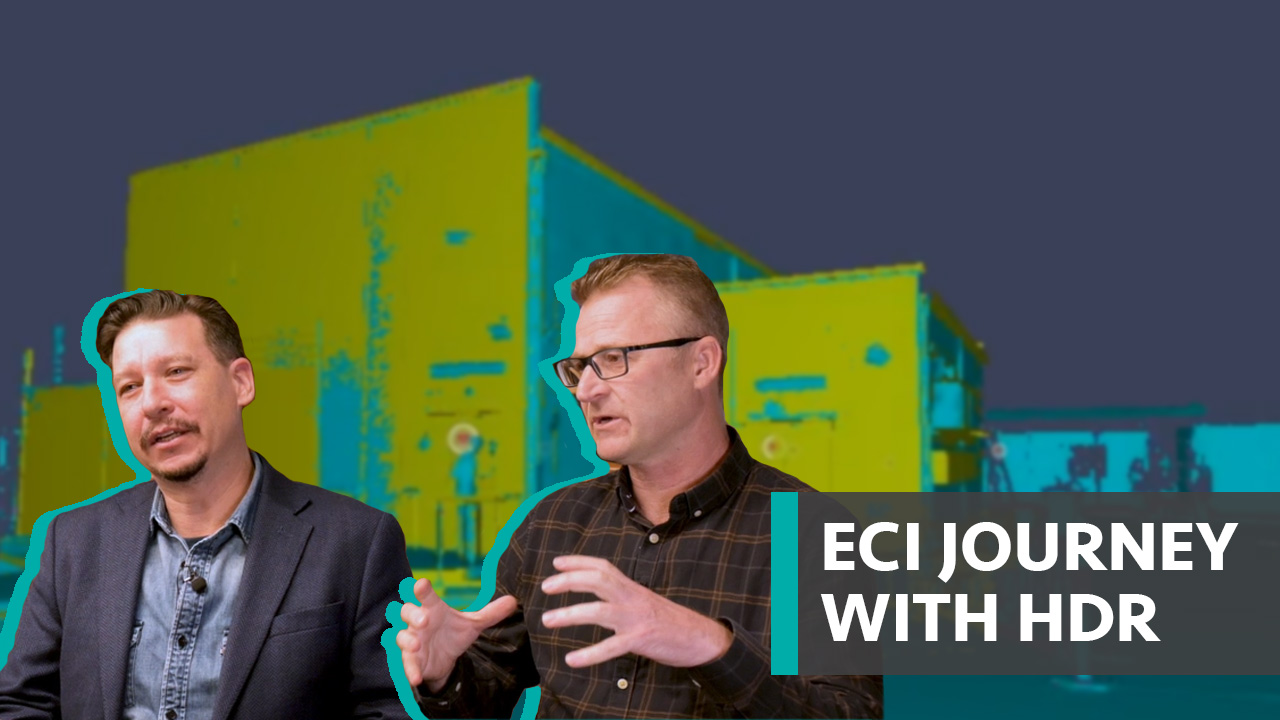
See some of our ECI work
Microsoft | MEL05 Data Centre, 12-week ECI
- Removed secondary steel and use of structural ceiling (saving $13m)
- Rationalised COLO design to use ceiling hung HAC containment (saving $500k per COLO)
- Rationalised foundation design (saving $500k)
- Improved construction site safety through reduction of at-height works using prefabricated external stair cores and roof enclosures
- Offered an improved approach to waterproofing
- Rationalised approach to fire rating.
Scape | Leicester St Student Accommodation, 12-week ECI
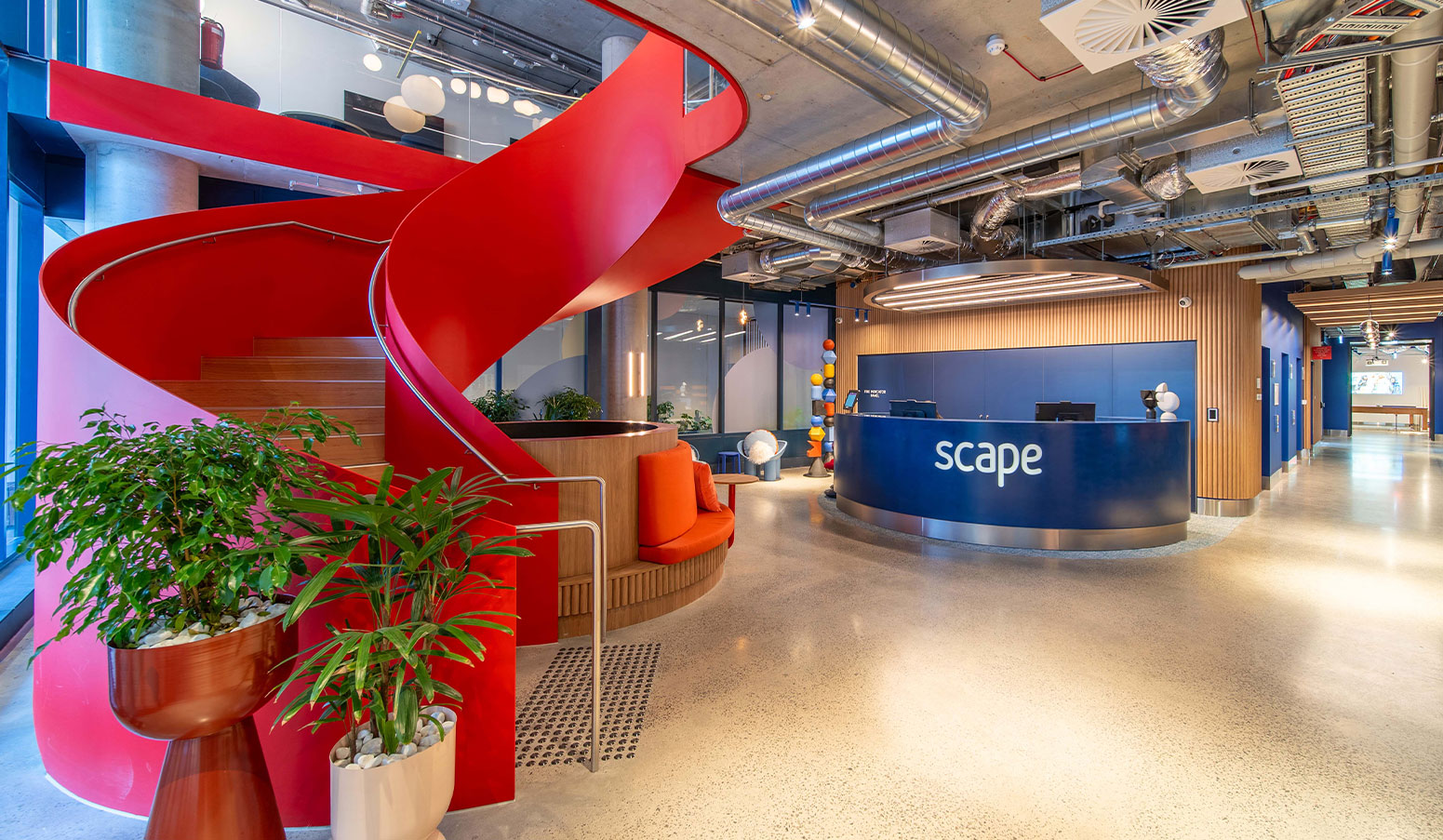
- Rationalised façade design from GRC to pre-cast, resulting in $3m in savings
- Optimised services design, thereby reducing basement area and extent of earthworks required
- Changed the EMS/BMS system to a more efficient system and found significant savings on joinery reductions, carpets, and tiles
- Streamlined room layouts to allow for prefabricated bathrooms (PODS) to accelerate the program and procurement schedules
- Optimised the prefabricated bathroom design, reducing number of doors and access panels.
Contact us for more project examples or to find out more about engaging Kapitol for an ECI.