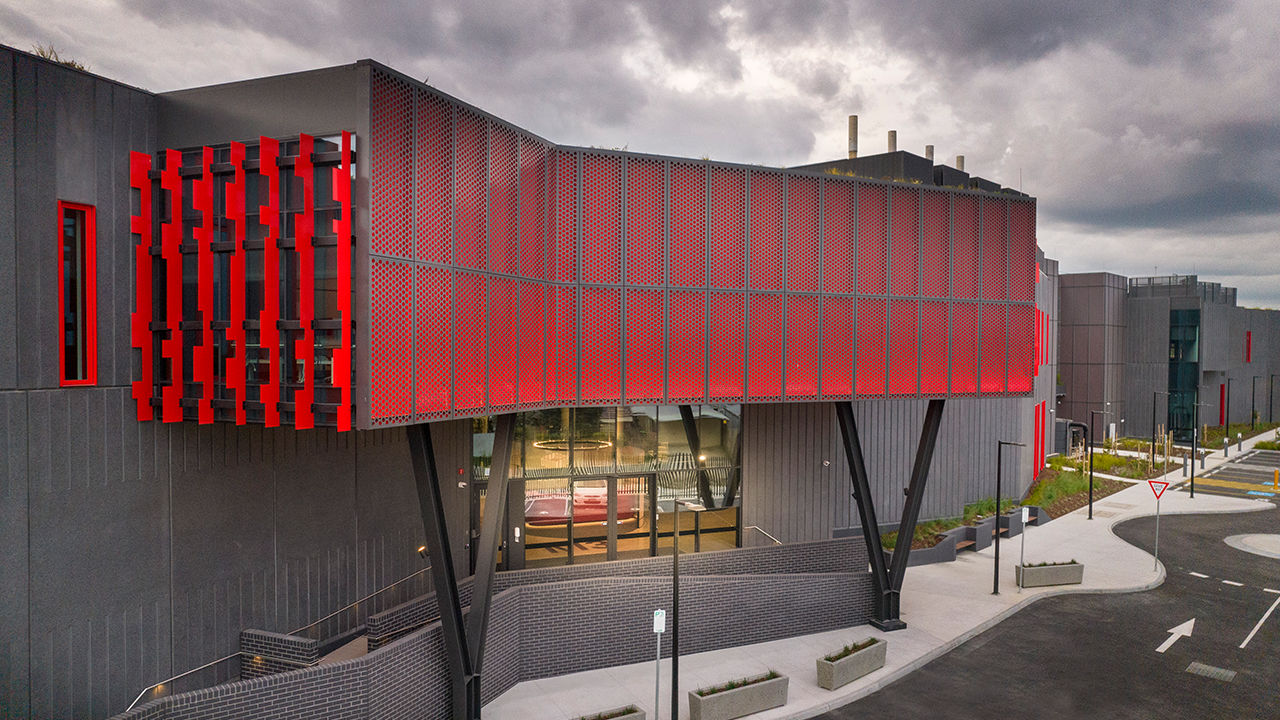
Share this story
Recent Australian research has identified weatherproofing and cladding-related issues as the most common types of construction defects. At Kapitol Group we’re not exempt from these challenges, we make mistakes, but we want to avoid making the same mistake twice.
This objective is realised by people like Dee Aydin, our highly experienced Façade Coordinator. As an architect with extensive local and international experience, Dee shares her layered perspective that melds the conceptual dimension of design with the practical realities of construction.
With her willingness to ask questions of subcontractors, manufacturers and colleagues Dee demonstrates an awareness of the errors and oversights that she has seen play out across the design, fabrication and installation phases.
Façade Coordinators often perform in a project-to-project capacity, however, Dee works continuously across the entire organisation to generate improvements through several key areas:
Facades attract attention
Façade and cladding systems are critical to the performance and user experience of a building, from energy efficiency to natural light and longevity. And of course, issues associated with weatherproofing have prompted changes to the National Construction Code, acknowledging the health and structural ramifications caused by leaks and moisture.
The external and internal building features interact and require an integrated approach. This necessity has not always been fully embraced, as Dee explains, “façade interfaces or subframe joints can't be checked at the end of the job as they’ll be covered with finishes. Interfaces and joints are where leaks most commonly occur.”
To tackle this, Dee has worked with teams to implement Hold Points in the Inspection Test Plan (ITP) to check the quality of installation for interfaces and joints before the programme moves on and the work becomes concealed. Dee is working to replicate this intervention to prevent waterproofing issues.
Leaky lessons
As part of the Quality team at Kapitol, Dee not only supports the implementation of the Quality System and the development of project-specific Quality Checklists, she also works alongside Project Coordinators to interrogate drawings and documentation, looking for detail inconsistencies or specification gaps. Unlike with services, for example, where digital technologies support clash detections, Dee explains that “finer details like caulk lines around the external glass are often absent from architectural drawings but of crucial importance to the built outcome.” This is a fine detail that is easily overlooked if never pointed out.
In her presentations to colleagues, Dee shares images from her catalogue of errors that she has recorded from sites. She uses these examples to demonstrate what to look out for. Dee’s case studies starkly exhibit what can go wrong, however, Dee steps through the key steps to avoid these mistakes and encourages conversations and ideas from the experiences of others.
The complexity and precision required in delivering high-quality façades and cladding comes down to millimetres. Many people are involved in the process and Dee engages with all of them, including compliance consultants. Sometimes she even adds inspection items to their lists to ensure that Kapitol projects meet every standard. Captured lessons are continually fed into Kapitol’s Integrated Management System, securing the knowledge for future projects.
Technically speaking
Having previously worked with a commercial aluminium window installer, Dee understands that seemingly minor workarounds on site can have major ramifications for the product's efficacy, leaving the building's envelope open to a raft of issues. To counter, this Dee has been engaging with manufacturers towards enhancing the team’s access to and understanding of the technical specifications of the cladding and façade products.
The Kapitol office has welcomed manufacturers of glazing, façade and sealant products to present on common pitfalls and how to get the most out of their products. Dee advocates for this shift from manufacturers working solely with subcontractors to working directly with the builders. The improved accountability and quality is helping to spread the responsibility and opportunities for a defect-free installation.
Dee’s approach is informed by experiences that are applied to support optimal façade and cladding outcomes. This increase in knowledge, awareness and confidence means more team members on site interrogating the details and asking the questions that deliver high-quality buildings – inside and out.
This objective is realised by people like Dee Aydin, our highly experienced Façade Coordinator. As an architect with extensive local and international experience, Dee shares her layered perspective that melds the conceptual dimension of design with the practical realities of construction.
With her willingness to ask questions of subcontractors, manufacturers and colleagues Dee demonstrates an awareness of the errors and oversights that she has seen play out across the design, fabrication and installation phases.
Façade Coordinators often perform in a project-to-project capacity, however, Dee works continuously across the entire organisation to generate improvements through several key areas:
- Project team support
- Peer-to-peer education
- Direct engagement with manufacturers.
Facades attract attention
Façade and cladding systems are critical to the performance and user experience of a building, from energy efficiency to natural light and longevity. And of course, issues associated with weatherproofing have prompted changes to the National Construction Code, acknowledging the health and structural ramifications caused by leaks and moisture.
The external and internal building features interact and require an integrated approach. This necessity has not always been fully embraced, as Dee explains, “façade interfaces or subframe joints can't be checked at the end of the job as they’ll be covered with finishes. Interfaces and joints are where leaks most commonly occur.”
To tackle this, Dee has worked with teams to implement Hold Points in the Inspection Test Plan (ITP) to check the quality of installation for interfaces and joints before the programme moves on and the work becomes concealed. Dee is working to replicate this intervention to prevent waterproofing issues.
Leaky lessons
As part of the Quality team at Kapitol, Dee not only supports the implementation of the Quality System and the development of project-specific Quality Checklists, she also works alongside Project Coordinators to interrogate drawings and documentation, looking for detail inconsistencies or specification gaps. Unlike with services, for example, where digital technologies support clash detections, Dee explains that “finer details like caulk lines around the external glass are often absent from architectural drawings but of crucial importance to the built outcome.” This is a fine detail that is easily overlooked if never pointed out.
In her presentations to colleagues, Dee shares images from her catalogue of errors that she has recorded from sites. She uses these examples to demonstrate what to look out for. Dee’s case studies starkly exhibit what can go wrong, however, Dee steps through the key steps to avoid these mistakes and encourages conversations and ideas from the experiences of others.
The complexity and precision required in delivering high-quality façades and cladding comes down to millimetres. Many people are involved in the process and Dee engages with all of them, including compliance consultants. Sometimes she even adds inspection items to their lists to ensure that Kapitol projects meet every standard. Captured lessons are continually fed into Kapitol’s Integrated Management System, securing the knowledge for future projects.
Technically speaking
Having previously worked with a commercial aluminium window installer, Dee understands that seemingly minor workarounds on site can have major ramifications for the product's efficacy, leaving the building's envelope open to a raft of issues. To counter, this Dee has been engaging with manufacturers towards enhancing the team’s access to and understanding of the technical specifications of the cladding and façade products.
The Kapitol office has welcomed manufacturers of glazing, façade and sealant products to present on common pitfalls and how to get the most out of their products. Dee advocates for this shift from manufacturers working solely with subcontractors to working directly with the builders. The improved accountability and quality is helping to spread the responsibility and opportunities for a defect-free installation.
Dee’s approach is informed by experiences that are applied to support optimal façade and cladding outcomes. This increase in knowledge, awareness and confidence means more team members on site interrogating the details and asking the questions that deliver high-quality buildings – inside and out.
Latest News
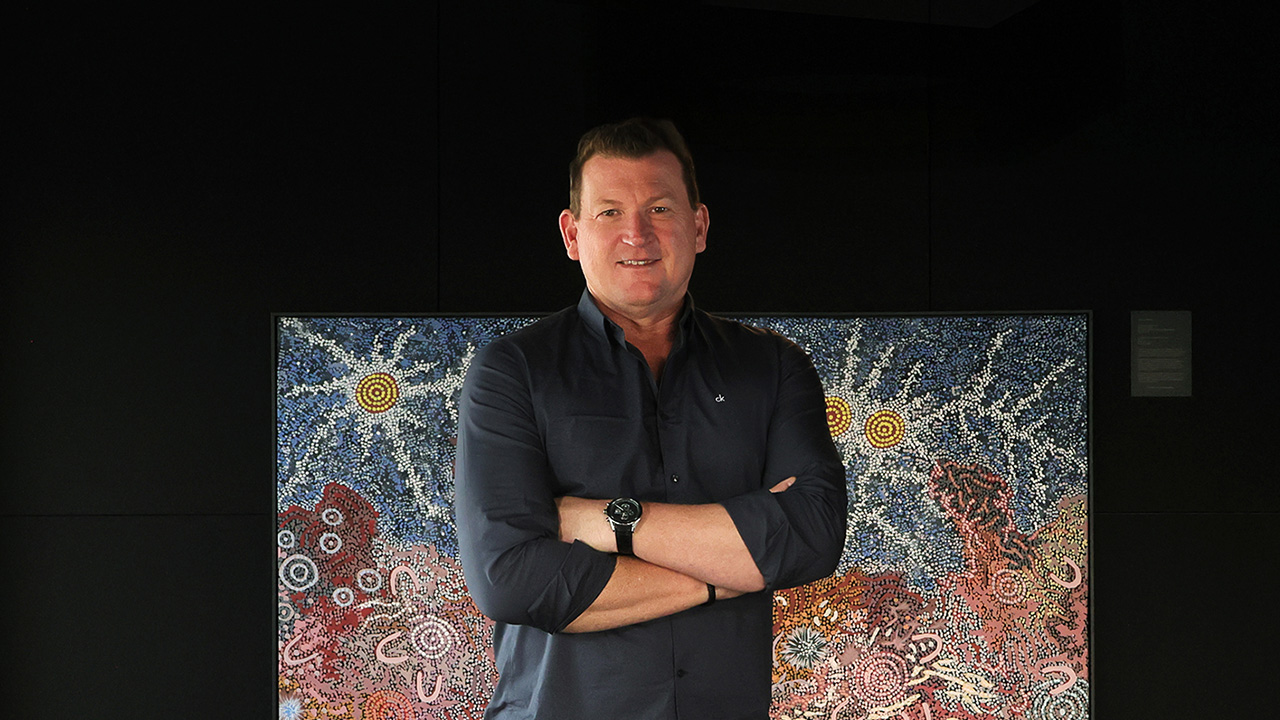
I Am Kapitol: Head of Health and Safety, David Spackman
David Spackman recently joined Kapitol as Head of Health and Safety, a critical role that aligns directly with our vision to transform the construction industry
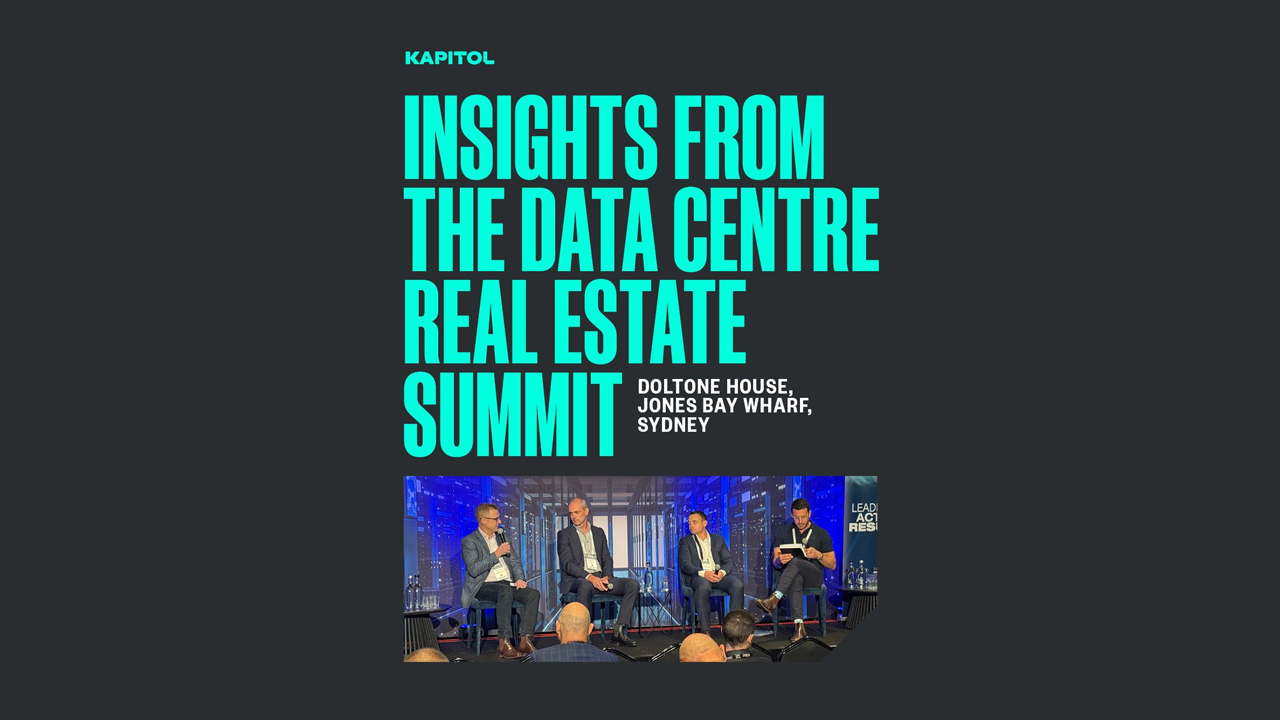
Insights from the Data Centre Real Estate Summit
Kapitol joined industry leaders at the Data Centre Real Estate Summit in Sydney to explore the future of scalable data centre delivery.
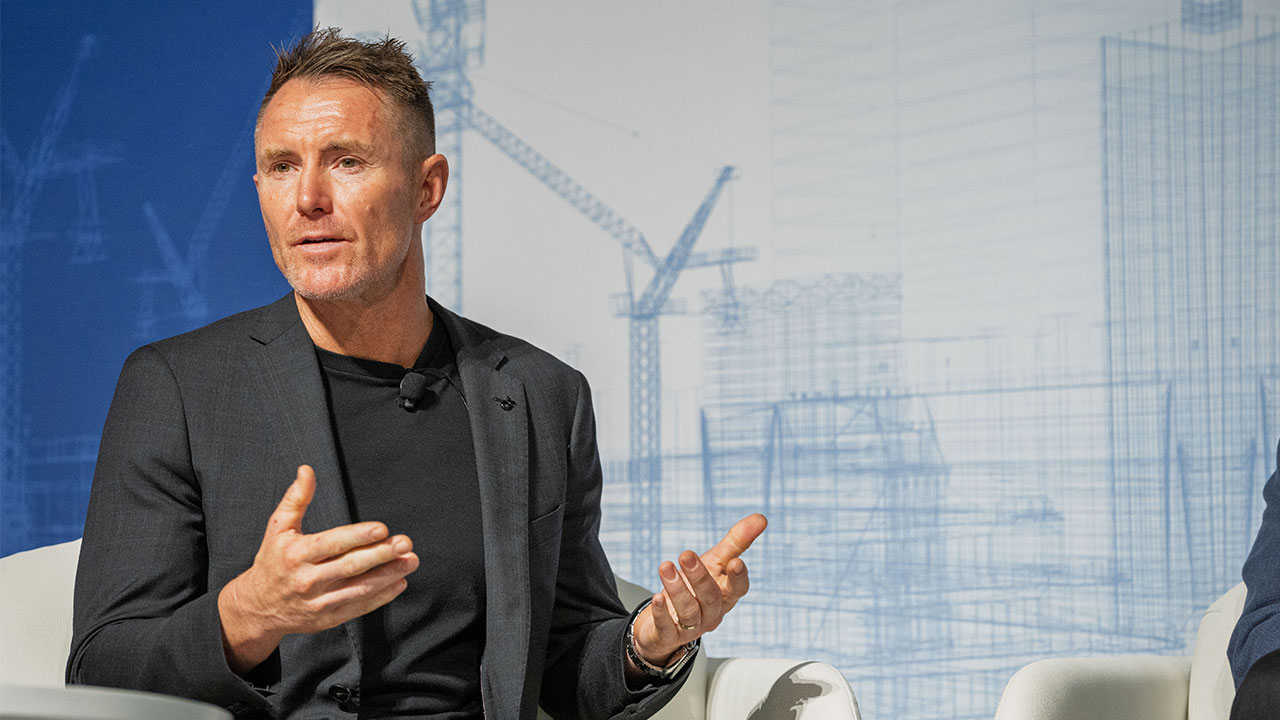
BIM & AI Reshaping Construction's Future - FCON 25
Kapitol's Head of Design & Digital Engineering, Kevin Hogan, joined industry leaders to discuss how digital transformation, BIM and AI is reshaping construction