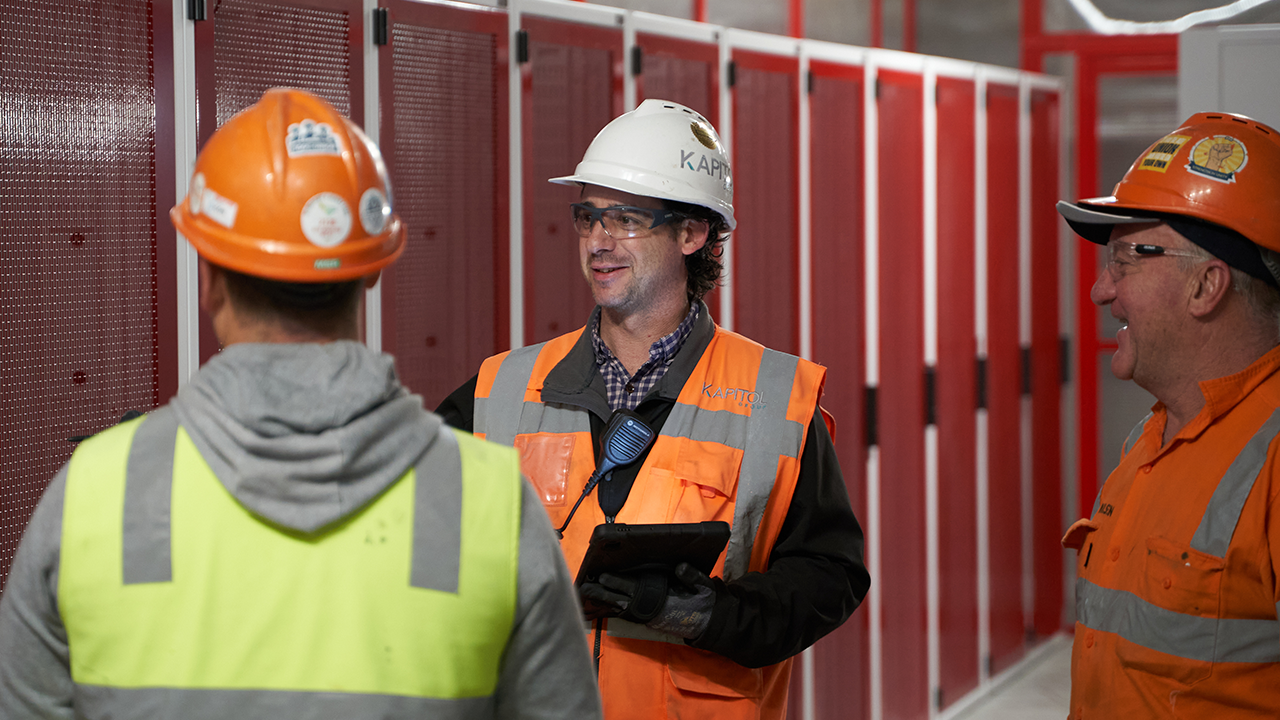
Share this story
Kapitol Group is on a journey to address a huge, construction sector-wide issue – quality.
Quality is the ongoing process of building and maintaining consistent:
✅ systems,
✅ plans,
✅ relationships,
✅ services, and
✅ fulfilling stated and implied results with the goal of customer satisfaction.
A year ago, we started to see a significant change in the quality mindset throughout our company and the benefits we can embrace building a powerful quality culture. Our quality team is progressing significantly on this journey to fortify our quality systems processes and improve the construction industry. These are some of the ways we’re doing this.
Meet the Team
Our Quality team is made up of six individuals with expertise in key areas, who focus on continually improving our operating methods, identifying training opportunities and systematically reporting the quality health of our company and projects. Additionally, the team regularly collaborate with industry consultants, such as TTW Façade, plumbing inspectors, and waterproofing specialists - to ensure that our external checks complement our internal quality measures and meet our company vision.
Continuous Improvement Strengthens our Future
Committed to enhancement, we are driven to learn from experiences during past projects and make necessary changes to our operating methods. Our quality team have observed, on previous projects, that some of our subcontractors can become complacent in carrying out their tasks, or are resistant to change and technology, which can lead to potential dangers and costly implications. Our quality team are dedicated to inspire positive change, streamline processes, motivate accuracy, eliminate waste and work with each area of our company to create the most efficient practices.
Addressing Design Challenges
Recognising the paramount importance of the planning and design stage, we have taken proactive measures to address design challenges head-on. Close collaboration with architects, consultants, and subcontractors enhances the process, and identifies any potential issues at the earliest opportunity. Our in-house design team, in collaboration with our sister company Resolve, and our subject matter experts identify where changes or modifications to the design, drawings or specifications are required. We use the latest BIM (Building Information Modelling) software to create 3D models of the intended build to aid in identifying any risks, clashes, issues, faults and required changes. Innovative design from the outset drives construction quality, enabling issue prevention throughout the lifecycle of a project.
Continuous Learning and Improvement Process (CLIP)
Our quality team plays a vital role in educating our staff and trades on various aspects of construction quality. Through our Continuous Learning and Improvement Process (CLIP), our quality team works closely with other departments to help all employees gain a deeper understanding of the design process, trade requirements, and key factors that contribute to quality outcomes. This is done through sharing lessons learned, and converting those lessons into a library of quality checklists and into a formal training and development program to ensure errors are not repeated and our high level of quality standards are upheld across the business. In the last 12 months alone, we have increased our converted ‘Lessons Learned’ into checklists by 295%!
CLIP in Action - Waterproofing
Our recent improvements to our waterproofing benchmarks is an example of our CLIP in action. When one of our site teams experienced air pockets and blistering in the waterproofing membrane on the roof of their project, they communicated the results of their investigation via Yammer, and during our monthly quality meetings, so other sites learned, and we were able to ensure future waterproofing of roof slabs do not encounter the same costly problem. The act of sharing lessons learned, or any honest mistakes from team members, inspires others to share their stories companywide resulting in Kapitol Group, and our subcontractors, updating ITP (Inspection Test Plans) checklist templates.
In 2023, the innovation and impact of Kapitol Group’s “CLIP” has, so far, saved $600k preventing errors, defects, re-works, and additional materials and this is only the tip of the iceberg.
Inspection Test Plans
To ensure consistent quality across projects, the quality team has applied a robust reporting system. Inspection Test Plans (ITPs) are the quality checklists our subcontractors, and project teams, closely work together to develop prior to the subcontractor working on our construction projects. Through regular updates to our ITP templates in our IMS (Integrated Management System) library and leveraging innovative powerful software tools like Visibuild, we have achieved greater transparency, accountability, and collaboration with our subcontractors. After testing various systems, we have partnered with Visibuild to develop an ITP management platform that will change the Quality Culture across the construction industry. Setting well-defined tasks within every ITP captures all critical risks, key measures, hold points and verification attachments offering a central source of quality data including detailed dashboards and subcontractor progress reports. This streamlined approach emphasises the importance of quality record management holding subcontractors accountable to meet Kapitol Group's project requirements, legislative standards, manufacturers specifications and the clients' expectations.
CLIP in Action - Piling
During piling coordination on one of our projects, a challenge arose. The team discovered fast wheels, connected to pile cages, detaching when they contact rough socket walls during the cage insertion process. Through collaboration with subcontractors, the site team devised a solution. This valuable experience was shared on Yammer (our internal comms channel) for all project sites to review. This experience resulted in an immediate update to our Piling ITP template and was integrated into VisiBuild as a mandatory step, for all future piles, to prevent recurrence. Ramifications for an issue like this is costly. This lesson learned has also been included in our Learning and Development program, to help educate our team about the significance of piling operations, the power of sharing their lessons learned and the true value of Quality and Continuous Improvement.
Conclusion
Kapitol Group's quality team is committed to improving the construction industry and promoting our company vision. The Continuous Learning and Innovation Process has helped sustain our growth, resulting in productivity gains that have allowed us to take on higher value construction projects in the 5 year’s Kapitol has been operating. We are still learning and refining our journey towards our vision to 'build the best buildings'. We’re delighted with the progress we’re making and hope to inspire others in the industry to learn and adopt a similar quality mindset to help to improve the construction industry, for a better life.
Latest News
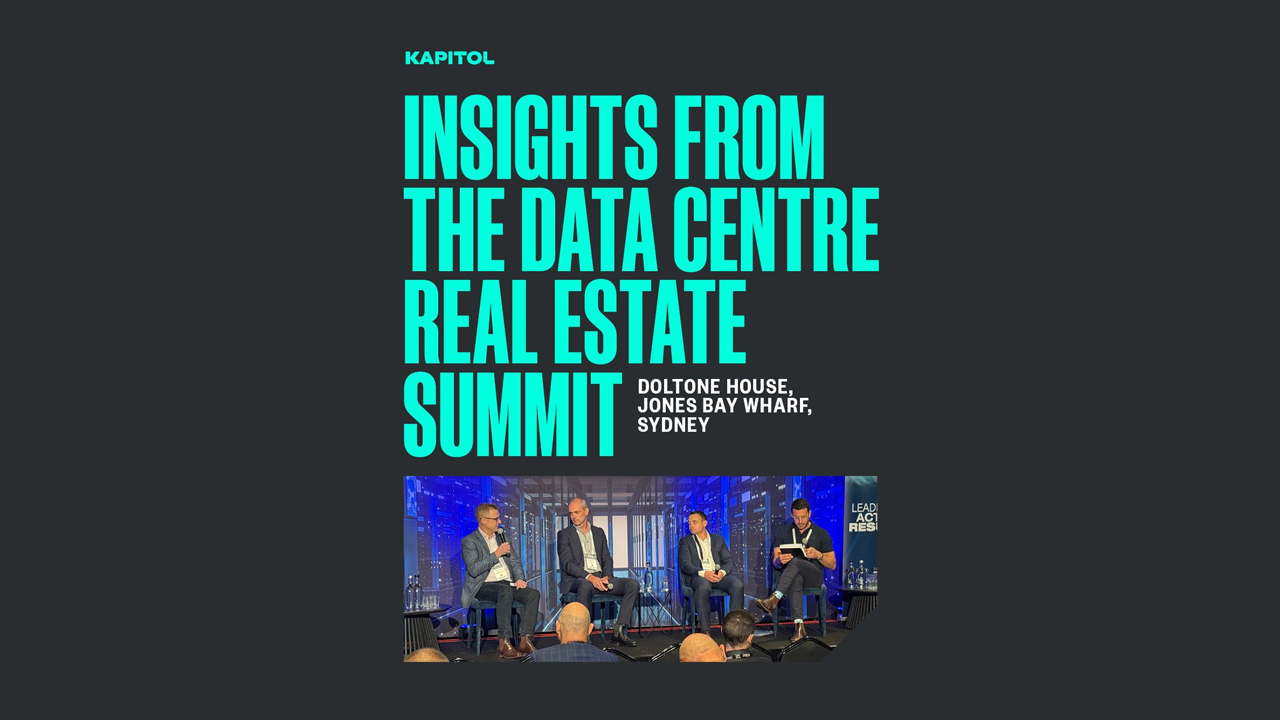
Insights from the Data Centre Real Estate Summit
Kapitol joined industry leaders at the Data Centre Real Estate Summit in Sydney to explore the future of scalable data centre delivery.
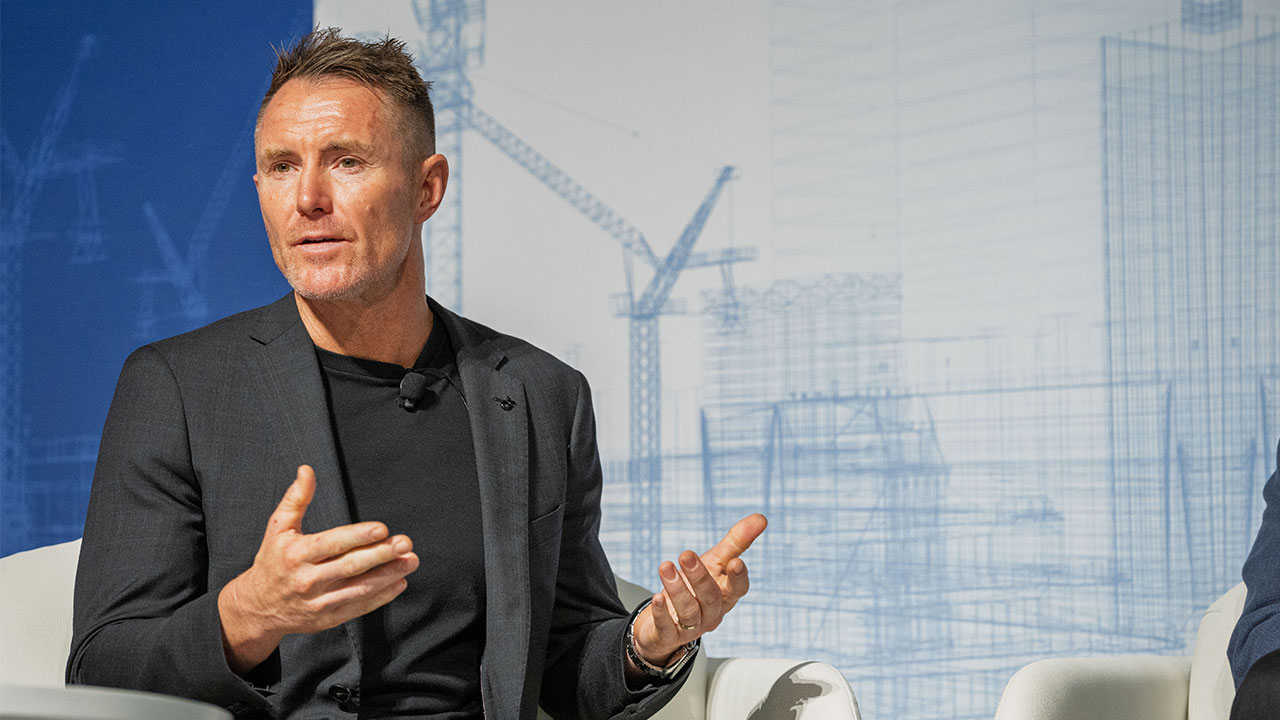
BIM & AI Reshaping Construction's Future - FCON 25
Kapitol's Head of Design & Digital Engineering, Kevin Hogan, joined industry leaders to discuss how digital transformation, BIM and AI is reshaping construction
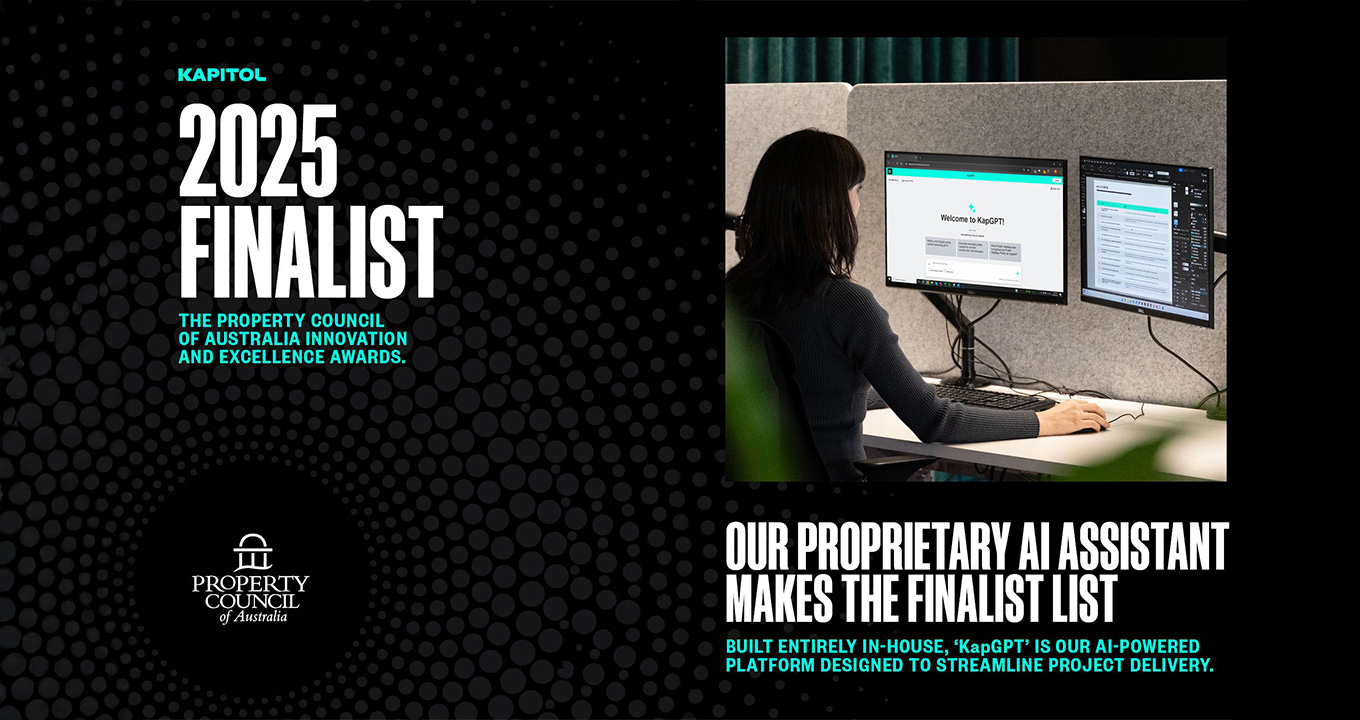
KapGPT: Finalist in Innovation Awards 2025
Kapitol Group continues to advance the way construction is delivered through the development of future-focused digital tools like KapGPT.