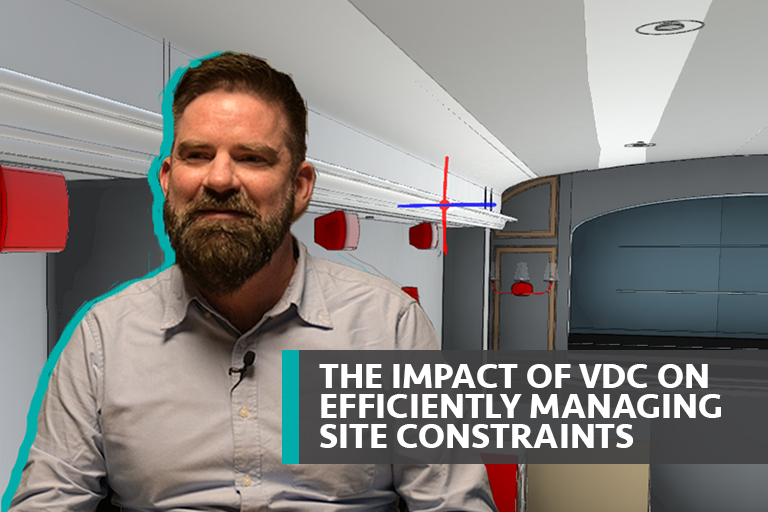
Share this story
Virtual Design & Construction (VDC) is used on every Kapitol building project. ‘Model before we build’ has become the backbone of how we’re improving quality and safety outcomes.
In the last 12 months we’ve commenced work on four new construction projects in Melbourne’s CBD—each with significant site constraints, and heritage façade retention requirements which need to intersect seamlessly with new construction.
Here’s a short case study of the challenges we recently faced on one of these projects, a high-end restaurant; what we did, and what we’ve learned for work on future site-constrained building projects.
The challenge
Our initial plans for the restaurant's Level 01 structural columns needed adjustment due to constraints related to the retained facade. We had to move the columns by 150mm relative to their original position to accomodate landing of the columns on the new floor slabs as required by the structural designer. This adjustment impacted our partition setting-out and has a flow on to the design and installation of the wall-to-wall curved ceiling in this space.
Discovery through modelling
As we had modelled the intent and the as-built condition, and shared these models live with our design team, we were able to develop an adjusted 3D model of the design intent for this area within a day. The design team updated the model to reflect the adjusted design intent for this curved ceiling, resolving the issue with the geometry of the bulkhead and the need to adjust the cornice position. Viewing the changes in 3D also allowed for a quick client approval, as it was easy for Kapitol Group to explain the change to the client's design team.
Since the bulkdhead had a 14-week lead time and was quite expensive, early detection was criritical. Resolving issues before they appear on-site meant we could focus more on the quality and finishes of those spaces, which aligns with our vision - to build the best buildings.
The outcome
By detecting and resolving the issue early, we saved 12 weeks of potential delays and approximately $150,000 in additional costs. Given the tight programme for this project, this was a significant achievement. By taking the time to plan, test, and resolve the design in a virtual world, we saved what could have been a compromised outcome for all stakeholders.
Lessons learnt
This challenge, the outcome, and the lessons our project team learnt were shared company-wide on Kapitol’s internal communications channel, Viva Engage. By sharing their lessons, we’ve ensured this issue isn’t replicated on another similar project. An issue we were able to catch early this time will hopefully not even happen again next time.
This challenge also demonstrates the power of modelling on every construction project, no matter the size. This project isn’t our largest in scale but it’s very complex so we’ve invested in having a dedicated digital engineer working side-by-side with our project team to continuously update the model as required and to help resolve issues, such as potential clashes, in real time before they impact the site. This is just one of many potential issues that have been mitigated by resolving the design in a virtual world before commencing building in the physical world.
To learn more about our Design & Digital Engineering team click here.
Latest News
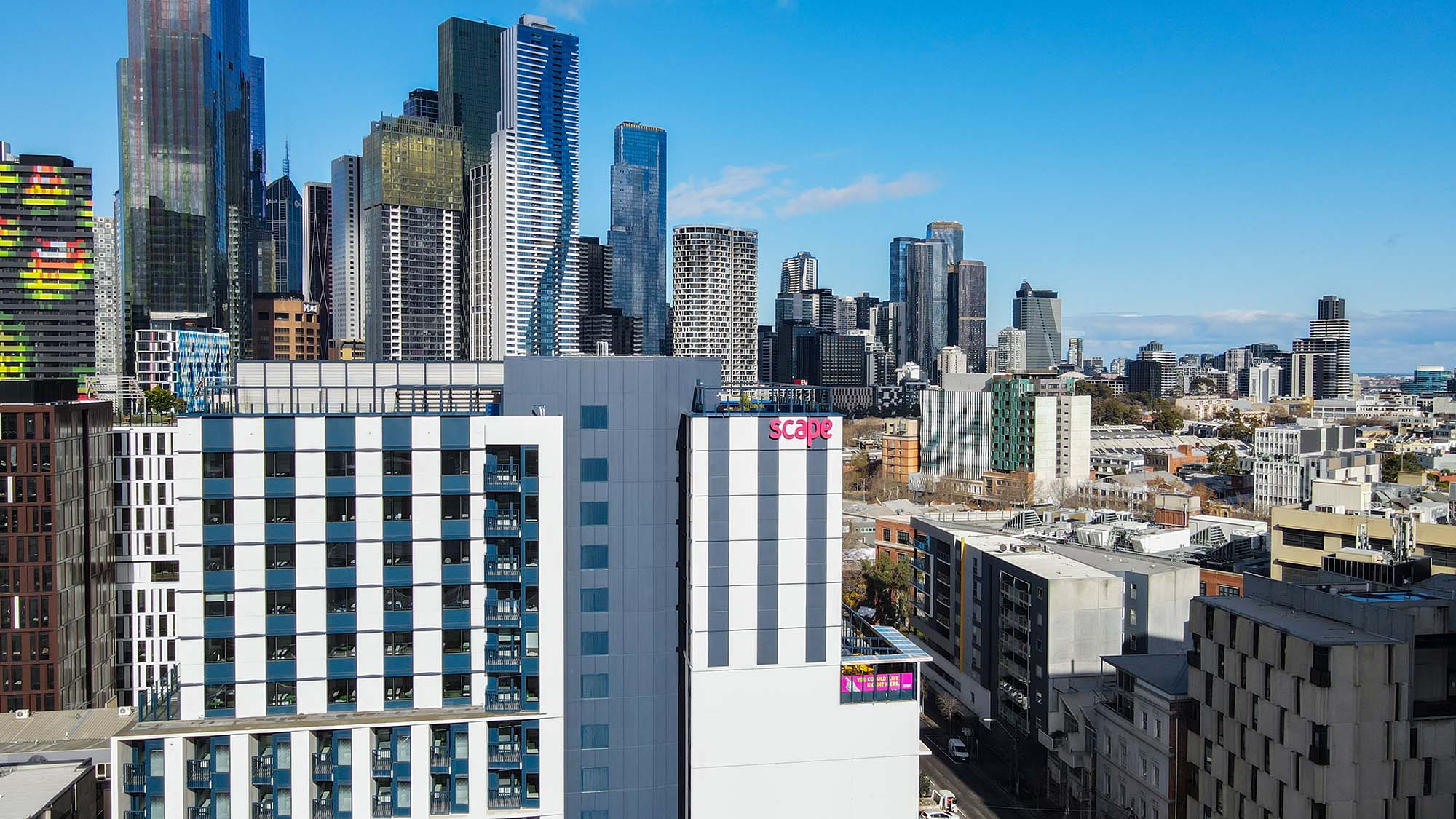
Scape Leicester St - Clean and Green Student Living
Located on the doorstep of University of Melbourne and the Melbourne Law School in the bustling student mecca of Carlton, the Scape Leicester Street project is one of Kapitol Group’s most acclaimed residential developments.
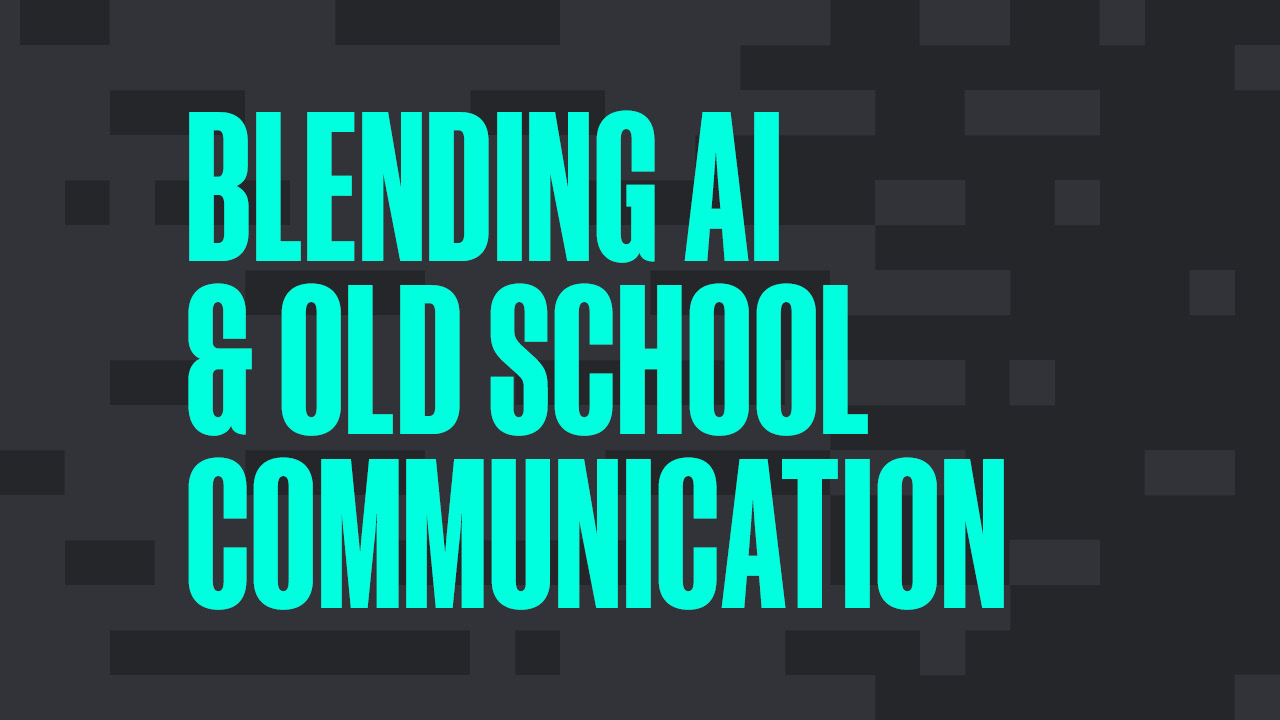
Blending AI & Old School Communication for Optimal Construction Delivery
Leading builder and construction industry innovator Kapitol, together with project management company Newbridge, are currently delivering 100MW through the second stage of NEXTDC’s M3 data centre in Melbourne.
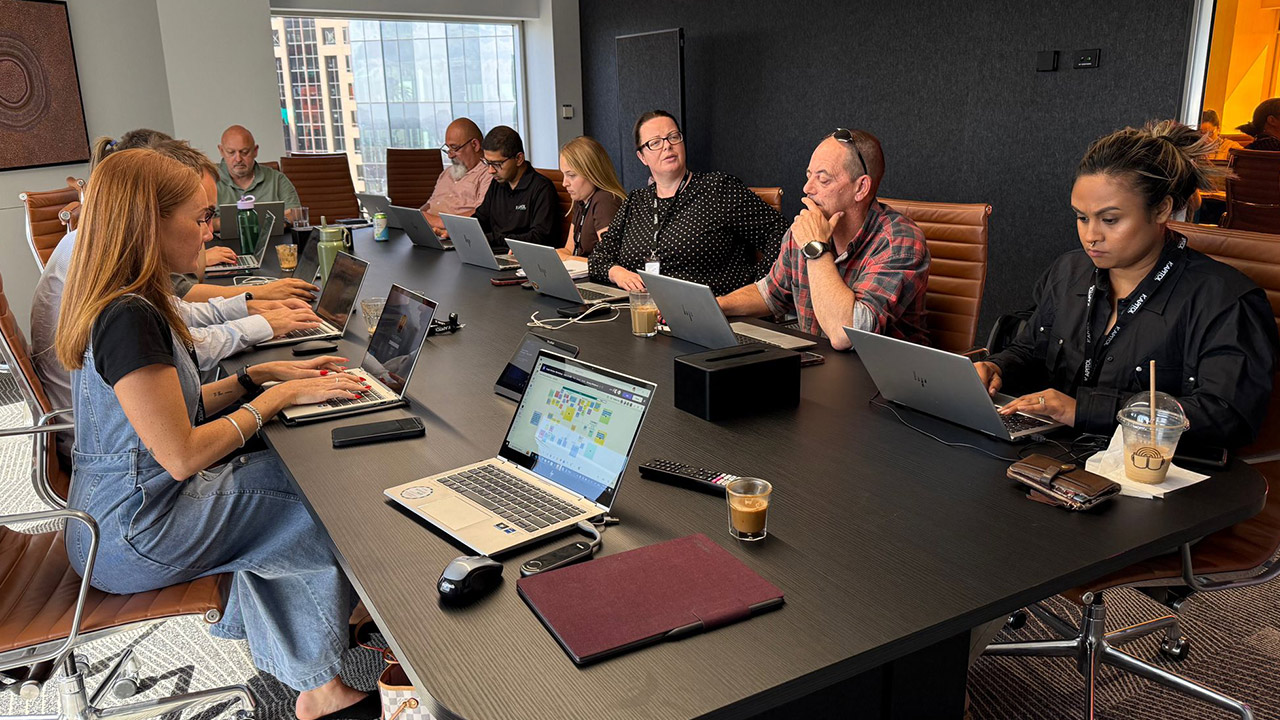
Enhancing Construction Quality with Ishikawa Sessions
Our Ishikawa workshops uncovered ideas to enhance construction processes, with 90 participants driving improvements for a successful 2025.