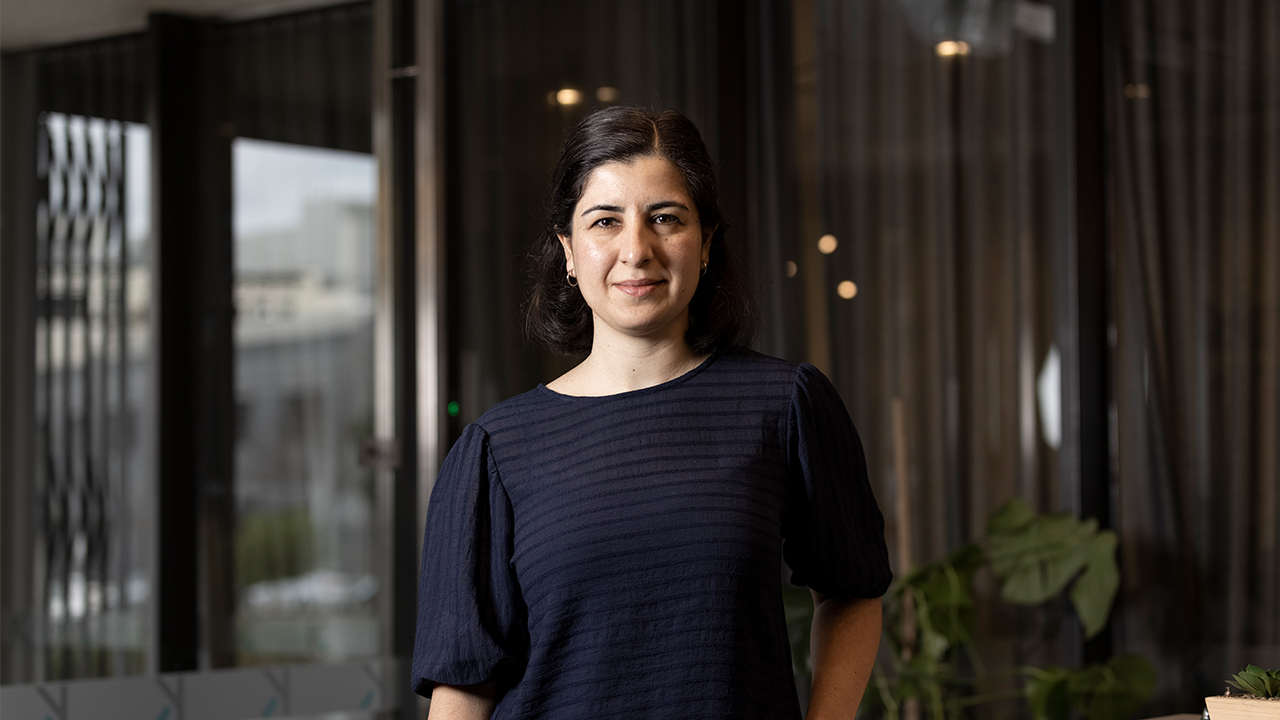
Share this story
Duygu Ede Aydin, Façade Coordinator – Kapitol Group
The imperative to decrease energy consumption and improve thermal comfort has driven a requirement to increase insulation and the airtightness of facades. Improved airtightness comes with a critical requirement to focus on vapour diffusion and condensation control. Moisture accumulation within building enclosure assemblies is unacceptable, posing risks to human health and increased maintenance costs.
At Kapitol we assess condensation risks early in design and progressively as the project moves through documentation to construction and handover phases. Our Façade Coordinator Duygu Ede Aydin (Dee) has provided architectural services on major construction projects in vastly different climates. Through engaging with different consultants in the field, Dee understands that there are different approaches and solutions which can be applied to tackle the issue. Modelling is critical to assessing how air and moisture will interact with different materials at different times of the year.
Surface condensation v interstitial condensation
Dee begins by explaining that there are two types of condensation: surface condensation and interstitial condensation. Surface condensation is often seen in our daily life, mostly on impermeable surfaces such as windows and particularly on winter mornings. We are less likely to see interstitial condensation as it occurs inside wall assemblies. Interstitial condensation causes mould growth, odours and poor air quality and can be dire for occupants, triggering asthmatic attacks, allergic symptoms, and respiratory infections. A quality building shouldn’t make you sick and doesn’t need to!
To assess interstitial condensation risks Dee focuses on external wall build-ups; currently many buildings have thermal insulation inside the stud wall to reduce heat loss through the external wall. However, if insulation is installed within the external cladding, the internal side of the external cladding/wall will be closer to the outside temperature. This is especially the case if the cladding is a low thermal insulator such as aluminium or concrete.
By fitting insulation inside the stud wall, heat transfer by glass wool or rock wool is reduced, but as Dee points out, the question we need to be asking is “how will vapour diffusion occur?” The direction of vapour drive needs to be understood to correctly plan the placement of materials within the assembly.
Risk factors
Dee explains that designers need to be alert to a number of risk factors. Risks include the orientation of the building, high water content of concrete, shade cast by neighboring high-rise buildings, the proposed mechanical system, make-up air, area of apartments, number of occupants and whether windows are operable. Ventilation is key here as relative humidity (vapour in the air) increases if we do not have enough ventilation (such as in winter when windows are more likely to be kept shut).
Whilst NCC 2019 FP6.1 provides some guidance on condensation risk management to really mitigate the risks, careful consideration of all these different factors is required.
Designing with condensation as a consideration requires understanding how a building is situated, how it will be used, but also walking it right back to the processes that inform construction. As Dee explains, consultants frequently assess materials from their individual perspective or field, resulting in advice which can be contradictory.
The importance of attention to detail
Attention to detail must be meticulous as demonstrated by the example Dee provides of an acoustic engineer who asked to separate the bathroom exhaust switch from the light, allowing the occupant to control the noise pollution. However, separating the light and fan switch potentially reduces the likelihood that the occupant will use the exhaust fan, increasing the house’s relative humidity. It means that designers not only need to consider how air and moisture behave but also how the users of the building are likely to behave.
One of the straightforward solutions Dee recommends is to review all materials and finishes with condensation in mind. Vapour control layers, insulation and paint all play a part in the performance of the building envelope. Kapitol works with façade consultants to check wall assemblies and calculate the risk of mould growth using WUFI, a Building Physics software package which can model the movement of heat and moisture.
Kapitol’s commitment to quality
The team at Kapitol is committed to leading in areas that often go unseen but represent the hallmarks of quality and leadership. In 2019 the NCC included condensation in its regulations and now in 2022, this has been expanded in the residential sector to include further condensation management provisions.
These include:
- A mould index added to the existing Verification Method
- Additional Deemed to Satisfy Provisions for vapour permeance of certain external wall and roof space materials and enhanced ventilation requirements for certain rooms and roof spaces
- Additional provisions for tightly sealed buildings in the existing Verification Method
Kapitol can easily absorb these changes as they are in line with existing practices. However as made clear by Dee, the interaction of materials, human behaviours and the external climate all need to be considered.
Building guideline changes should be read as interdependent rather than stand-alone. A change to air tightness standards may have implications for condensation, even though it is not explicitly stated. By taking a holistic approach the team at Kapitol is mitigating risks for owners and occupiers alike.
Latest News
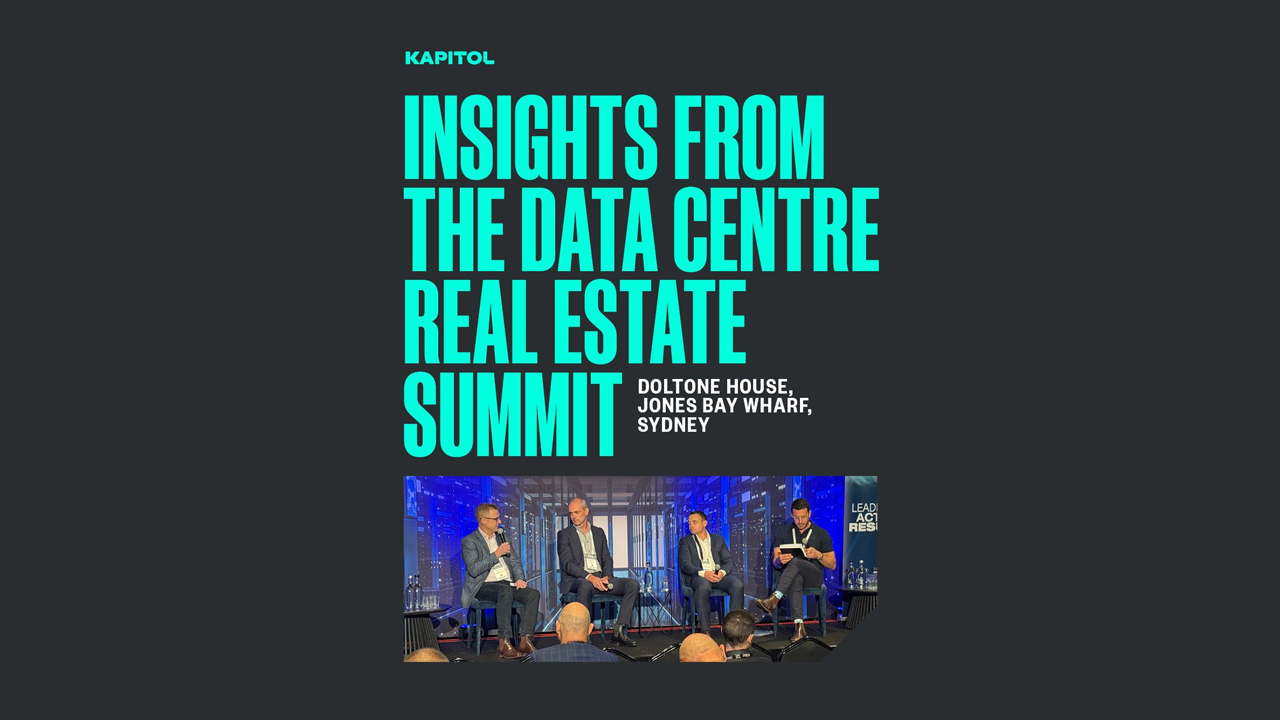
Insights from the Data Centre Real Estate Summit
Kapitol joined industry leaders at the Data Centre Real Estate Summit in Sydney to explore the future of scalable data centre delivery.
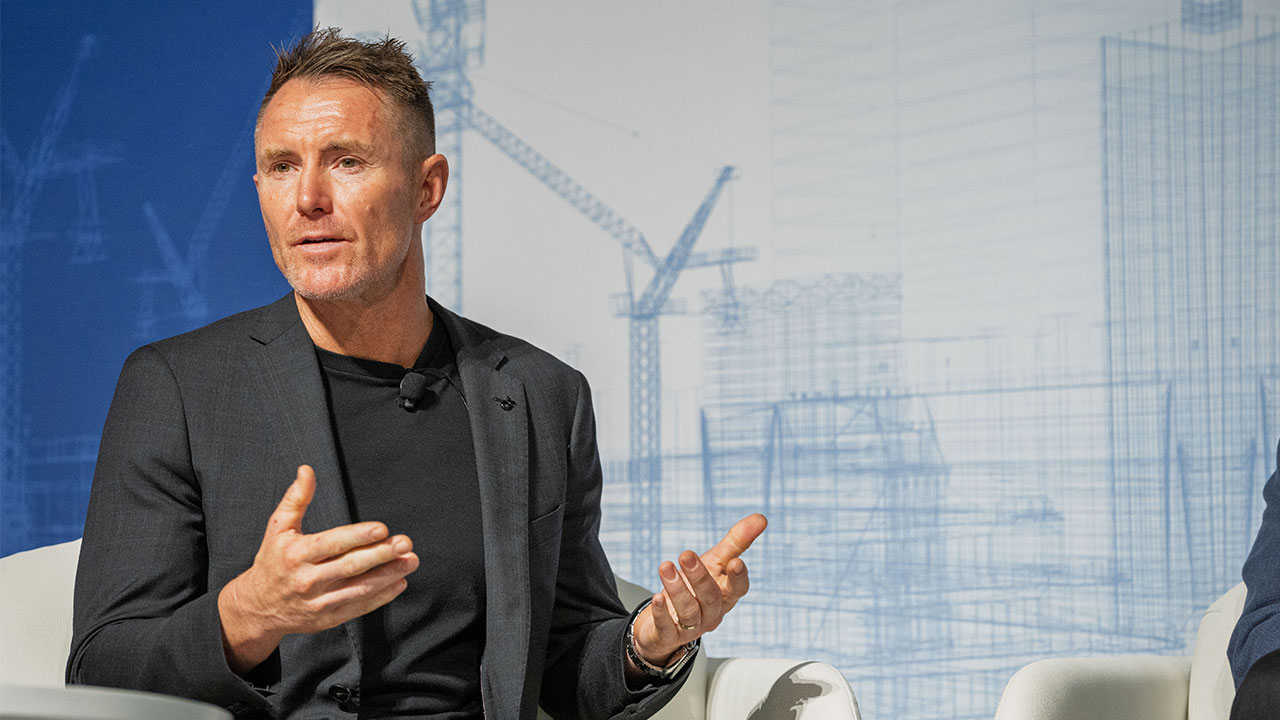
BIM & AI Reshaping Construction's Future - FCON 25
Kapitol's Head of Design & Digital Engineering, Kevin Hogan, joined industry leaders to discuss how digital transformation, BIM and AI is reshaping construction
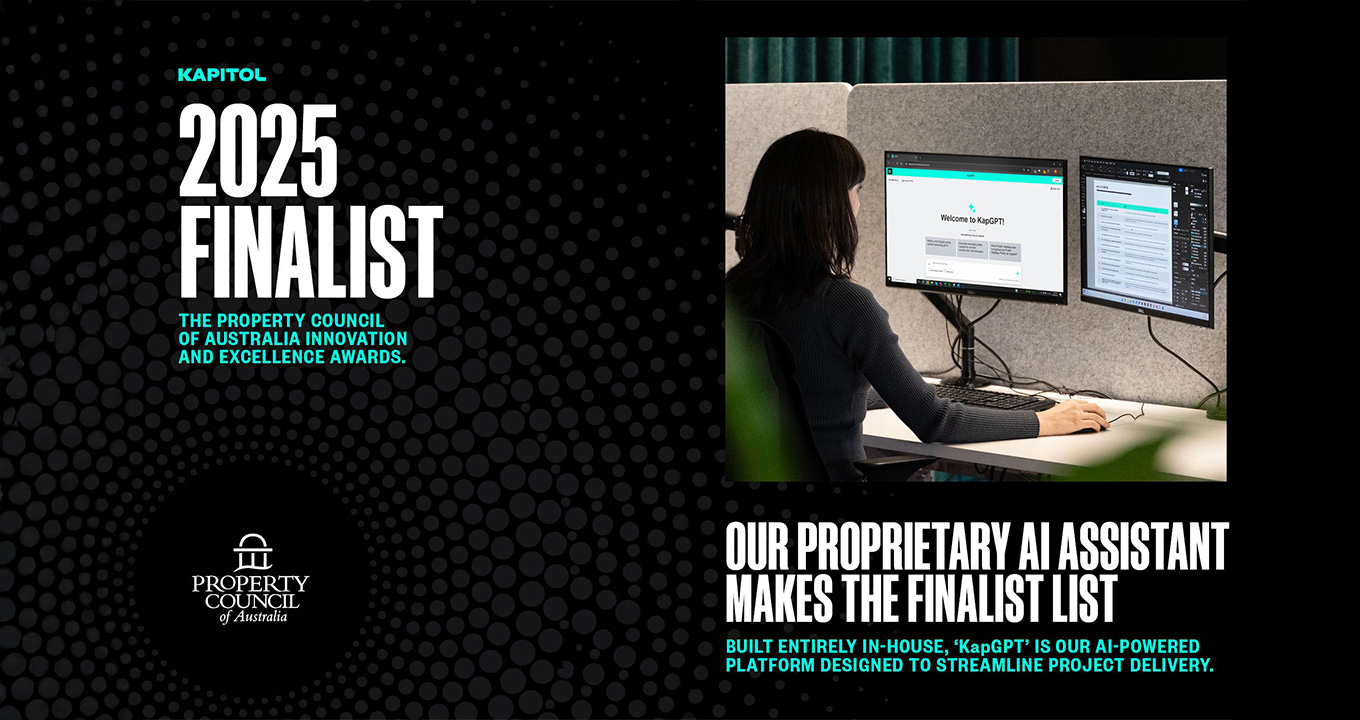
KapGPT: Finalist in Innovation Awards 2025
Kapitol Group continues to advance the way construction is delivered through the development of future-focused digital tools like KapGPT.